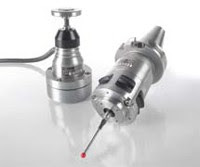
The company said its UTI 192 Universal Touch Probe Interface makes its probes compatible with CNC controls via a fast switching input.
The UTI 192 supports two lines Heidenhain 3-D touch probes, the TT tool touch probes and TS workpiece touch probes. This interface is designed to convert output signals of the Heidenhain 3-D touch probe to the machine control signals in accordance with IEC 61 131-2
Heidenhain said the probing functions that are actually available on the machine depend on the software cycles that are implemented in the respective control. The company offers cycles for automatic alignment and measurement of workpieces, workpiece presetting, and tool measurement on non-TNC controls.
The UTI 192 features a compact design, and can be fastened quickly on a standard mounting rail in the electrical cabinet. Heidenhain said it features a wide range of interfacing possibilities so that the touch probes can easily be connected to the different controls.