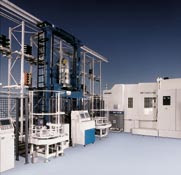
In today’s competitive CNC manufacturing environment, the need for quality is a given, and job shops often win or lose contracts based on per-part costs that vary by just fractions of a cent. Naturally, the promise of achieving cost-efficient, consistent machining results through the use of robotics and automation is attractive to large metalworking concerns and small job shops alike. But many managers considering automation wonder if the time is right for a change. Or, they worry that quality will suffer if they dare to automate the processes they currently rely on for profits.
Like any successful business venture, the move to automation is best approached by following a sequence of orderly steps. Being sure the time is right to make the move to automation can be accomplished in an orderly fashion as well. In fact, there are a number of “machining milestones” any manager can use as a yardstick to gauge a shop’s readiness for robotics. The first of these milestones is the attainment of stability—inherent reliability in the machining process being considered for automation.
Naturally, most shop owners facing automation probably worry at least to some degree about the potential downside. However, many organizations making the switch to automated CNC machine tools find that quality actually increases with the change. Without exception, these shops share one important trait in common: the machining process they are automating has been reliable from the start. John Burg, Automation Division manager for Okuma distributor Ellison Machine Tools and Robotics (Warrenville, Illinois), agrees with this assessment.
"Even ISO 9000 is not strictly about quality,” he says. “It’s more about deciding how you are going to standardize a process, then following through and executing that process according to your standardized plan. That’s also the key to successful CNC machine tool automation. Once you get the process in control and standardize operations, superior quality naturally follows.”
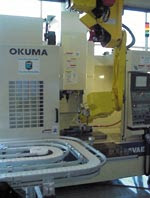
Getting Set Up
Equally important is the need for establishing a controlled process for performing setup. Many owner/operators facing the move to automation are concerned that they’ll incur extra setup requirements to facilitate the use of robotics. In fact, many new users of automated machine tools find that setup time is actually reduced. This is true because once the process is controlled, it is no longer subject to time-consuming variables such as operator preference.
Imagine a part running on the same machine over three shifts daily. Every morning, Operator A sets up his material to the left of his CNC milling machine. At the start of the second shift, Operator B arranges inbound material to right. Later that evening, Operator C stays with B’s material setup but adjusts machining speeds and feeds according to personal preferences.
“I’ve actually walked into shops and found operators working different shifts using their own CNC programs to run exactly the same parts on the same machines,” Mr. Burg recalls. With automation comes the necessity for consistency and controlled setup and working processes. The advent of systematic operations that prescribe material flow, tool selection, chuck type, gripper details, and a host of other parameters also eliminates the type of counter-productive Operator A, B and C scenarios outlined.
The need to tame unbridled fluctuations in rates to keep production—and profits—consistent is another indicator pointing to an impending move to automation. Users of manually loaded CNC machine tools have historically come to expect production rates to vary widely from shift to shift and day to day. In fact, variations in similar processes can vary as much as 30 percent. With automated cells in place, owner/operators typically find that production rates vary less than 5 percent from one shift to another.
As an example, Mr. Burg cited one application that had 14 identical machines operating on a 7-second cycle time to machine aluminum substrate components for computer hard drives. The variations measured from machine operator to machine operator essentially reflected their individual dexterity. While some operators consistently ran more than 2,000 pieces in an 8-hour shift, others could turn out no more than 1,200 good parts.
With automation, the process on all 14 machines immediately produced 4,000 parts per shift. Results were consistent from machine to machine and shift to shift, with variations limited to increments of no more than one-half of one percent. Similarly, tracking spindle uptime as a measure of productivity is another indicator that can clearly point to the need to move to automation.
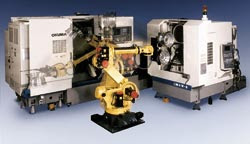
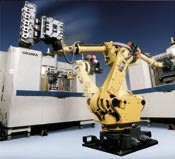
No comments:
Post a Comment